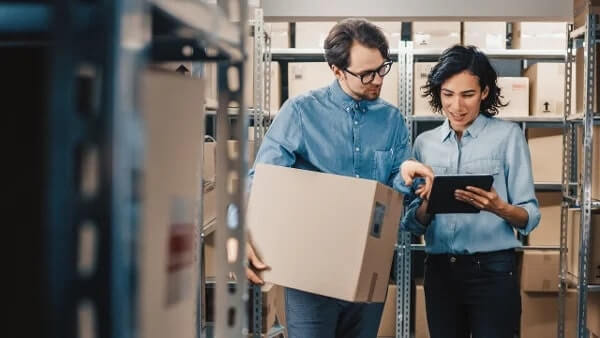
Mastering the mock recall procedure: A step-by-step guide
A detailed guide on the importance, common mistakes, and benefits of regular practice for safety and compliance
In the world of food and product safety, staying ahead of the curve is not just a competitive advantage but a moral imperative. With the proposal of FSMA 204, a groundbreaking piece of legislation, the bar for food and product safety and transparency is set to reach new heights. This new regulation introduces additional record-keeping requirements, placing a significant compliance burden on impacted parties. But the true intent of FSMA 204 goes beyond mere compliance—it seeks to create a fully transparent supply chain that ensures safer products for all. This ambitious goal aims to mitigate risks like foodborne illnesses and enhance consumer trust.
Now, combine FSMA 204 compliance with a robust and 'always ready' recall program, and you have a powerful combination that can help brands contribute to the realization of this transparent supply chain vision. The critical link here is the practice of mock recalls, a routine that trains your team to be fully prepared for swift and efficient recall management.
The bottom line is clear: traceability and readiness are essential components of a successful recall, all in the name of food safety. In this blog, we'll delve into the world of mock recalls, explore their significance, and discuss how they align with the broader mission of creating a safer and more transparent food supply chain.
Why mock recalls are essential
In today's fast-paced world, every second counts, especially during a crisis. For brands navigating the challenging terrain of a product recall, even a moment's hesitation can lead to wasted time and increased risks.
This is where mock recalls come into play. These simulated recall exercises prepare your team and familiarize them with the intricate steps and responsibilities required during an actual recall. Think of it as creating muscle memory so your response is immediate, automatic, and authoritative, without the need for detailed deliberation.
This begs the question: Is your company prepared should a product, food item, or food ingredient be recalled?
Without making mock recalls a routine practice for your business, you’ll be entering a crisis unprepared—which is a perfect storm for a catastrophic impact on your customers, employees, and brand. But, by routinely testing and fine-tuning your process and systems, you ensure your organization is ready to act when the time comes.
Conducting a consistent mock recall procedure has 3 significant benefits for brands. When implemented correctly, mock recalls help:
- Ensure product safety & quality
- Meet regulatory requirements
- Build consumer trust
Now that we’ve discussed why mock recalls are essential, let’s look at what it takes to build an effective mock recall strategy.
Steps to implementing a mock recall procedure
The goal of any mock product recall or food recall is to poke holes in your system, identify weak spots in your process, and highlight your deficiencies. This will help you make improvements along the way.
While there’s no doubt that you want to strive for perfection, mistakes are expected, and it’s better to get them out of the way now when your business’s reputation and your customer’s health and safety aren’t in jeopardy.
According to Quality Assurance Magazine, the keys to an effective mock recall are:
- Be realistic
- Be comprehensive
- Document everything
- Critique/review yourself and your system
- Assess the effectiveness of the mock recall
So, what are the recommended steps to prepare for a mock recall, and ensure food safety in the supply chain?
Step 1: Get management involved
It’s important that management is aware and on board with the mock recall, but unaware of when it will happen. Enlisting their support and participation is the only way to ensure that every employee takes it seriously. So, focus on the importance of practicing, and the long-term impact it can have on the company and its customers.
By practicing now, you can protect the business in the future.
Step 2: Build an effective recall management team
Once you’ve enlisted management’s participation, it's important to designate a crisis management team who'll be responsible for handling your recall process and communicating with partners along the supply chain. Nominate the recall coordinator and then designate the chain of command.
According to Food Manufacturing:
Your team needs to be well-rounded and will ideally include the heads of maintenance, engineering, food safety, quality assurance, and sanitation. If you have the luxury, you should also include a microbiologist, a chemist, or a toxicologist.
Step 3: Select a random product
If you’re trying to gauge the efficacy of your recall plan, systems, and processes, you can’t cheat by broadcasting to your organization that it’s going to happen. Like a fire drill, it needs to be conducted randomly, so that everyone treats it with the same seriousness they would in the case of the real thing.
So, on the appointed day, we recommend selecting one or more products and lot number(s) to be used for the mock recall. From there, provide a reason for the recall (stating this is a mock recall is okay). There are a variety of mock product recall scenarios (from widely distributed products to more targeted ones), and although you don’t want to incite a panic, you shouldn’t pick something that is too narrowly focused in scope. Testing different days of the week, hours of the day, multiple locations, regions, or even time zones are all good ideas.
Challenge your team. By doing so, you can accurately test how prepared your team and supply chain is for the real thing.
Step 4: Perform the mock recall
Once the mock recall has begun, it’s time to monitor your recall team as they track products via traceability procedures.
The team will be tasked with determining:
- The products involved (differing sizes and quantities may be in play here)
- The amount of affected product in the supply chain
- Where the product is
- Customers who have received the product
Ideally, your team would utilize product recall management software that automatically facilitates the process from investigation, identification, notifications, and recovery to record-keeping and reporting.
Step 5: Send notifications & monitor responses
Once you’ve created your distribution list and sent your communications (be sure to include an expected time frame to respond), you’ll need to start tracking responses and the time it takes for parties to respond. It’s important to gauge:
- Did recipients get the notification?
- Do you have good contact information?
- Were the instructions clear on how to act?
- Did people receive the notification but not understand the need to respond or how to respond?
- Was the product identification information clear?
- Was the correct product found?
- Were all the correct SKUs included in the responses?
- What other identifying information would be helpful?
- Were the instructions clear on what to do with the product? (Be sure to let them know that the product doesn’t have to be destroyed or sent back as this is just a test!)
- Did recipients respond within the expected time frame?
Step 6: Postmortem review & adjustments
Once your test has come to an end, you’ll need to see how effective your team was, and you’ll need to measure your effectiveness percentage. You can do so by comparing the recovered product amount to the amount in inventory. Your goal is to reach 100% reconciliation, but in all likelihood, it won’t be. You might even end up well above 100%!
We also recommend spending time calling and debriefing with those who responded and those who didn’t. Identifying aspects that work and areas that need improvement is important.
You’ll next want to spend time as a team reviewing your documentation and looking for areas to improve, such as:
- Internal or external communication issues
- Silos of information, incomplete information, or conflicting sources of information
- Incomplete or inaccurate contact information
- Team members or supply chain partners that failed to follow the recall procedures
- Issues with instructions and identification or labeling errors
- Lack of control over products that were put on hold
- Slow or inadequate responses
From there, take the necessary steps to rectify the issues and cover your exposure gaps.
Step 7: Practice
As we’ve stated throughout this piece, you don’t simply do this one time and consider your job done—you do so regularly.
According to Food Logistics:
As a general guideline, execute mock recalls every 12 to 18 months to identify any potential gaps and correct them. However, if a series of gaps are evident, you don’t want to wait a full year to conduct a mock recall again. Overall, it’s something that you want to make sure you’re doing on a frequent basis, that you’re taking action, and that you’re documenting it.
Remember, practice makes perfect.
Common mistakes to avoid
In the realm of mock recalls, several common mistakes can hinder their effectiveness and potentially compromise an organization's preparedness for real recall situations. One prevalent mistake is not involving all relevant stakeholders or failing to test both supplier and facility impact. It’s vital to test the accountability in reaction and resolution of your partners and external parties.
Effective recall management requires seamless coordination among various departments, such as quality control, legal, supply chain, and communication teams. Failing to include all relevant personnel in mock recall exercises can lead to miscommunication, delays, and confusion during a real recall. To avoid this mistake, it is essential to ensure that all key stakeholders are actively engaged in mock recalls, allowing them to understand their roles and responsibilities and fostering effective teamwork.
Another significant error to avoid is not updating the recall procedure regularly. As a business evolves, so do its products, processes, and potential risks. Neglecting to update the recall procedure regularly can lead to outdated or inadequate strategies that do not align with the current business landscape. Mock recalls should reflect the most current and relevant scenarios, including changes in products, suppliers, and regulations. Regular reviews and updates to the recall procedure help ensure that it remains robust and aligned with the organization's needs, providing an accurate simulation of real-world recall challenges.
A third mistake is overlooking documentation. In a recall scenario, thorough documentation is crucial for traceability, compliance, and post-recall analysis. Failure to maintain accurate and complete records during mock recalls can lead to difficulties in tracking product movements, verifying product disposition, and assessing the effectiveness of the recall process. To mitigate this risk, businesses should emphasize the importance of meticulous documentation during mock recalls, ensuring that they mirror the level of detail and precision required during an actual recall. Accurate records not only aid in compliance but also serve as a valuable resource for continuous improvement in recall procedures.
Benefits of regular mock recalls
Mock recalls offer a multitude of benefits, each contributing to the overall resilience and effectiveness of a business:
- They significantly enhance a company's readiness for actual recalls. By simulating recall scenarios, organizations can identify any weaknesses or bottlenecks in their recall procedures, allowing them to fine-tune their response strategies. This proactive approach ensures that when an actual recall situation arises, the team is well-prepared, reducing response time and minimizing potential damage to the brand and consumer safety. In essence, mock recalls are like fire drills for product recalls, helping organizations extinguish any potential crisis with speed and efficiency.
- The practice of mock recalls fosters enhanced team coordination. Effective recall management requires close collaboration among different departments, including supply chain, quality control, legal, and communication teams. Mock recalls serve as a platform for these teams to work together in a controlled environment, improving their understanding of each other's roles and responsibilities. This synergy is vital during an actual recall when swift and coordinated actions are crucial. The lessons learned during mock recalls not only enhance teamwork but also establish clear lines of communication, ensuring that the right information reaches the right people at the right time.
- Mock recalls promote a culture of continuous improvement in processes. Businesses that regularly conduct mock recalls are more likely to identify inefficiencies and areas for enhancement in their recall procedures. This ongoing process of evaluation and refinement results in increasingly efficient and effective recall processes, which can ultimately save time, resources, and reputation in the long run. The commitment to constant improvement also demonstrates a company's dedication to quality, safety, and consumer satisfaction, instilling trust among consumers and stakeholders. In a dynamic and ever-changing business environment, the ability to adapt and evolve is a significant advantage, and mock recalls play a pivotal role in this evolution.
Prioritizing mock recalls: A commitment to safety and regulatory excellence
The significance of mock recalls cannot be overstated when it comes to safeguarding the integrity and reputation of businesses. These simulated exercises serve as a vital tool in proactively identifying and addressing potential weaknesses in a company's recall process, ultimately minimizing the risk of costly and damaging product recalls. Mock recalls are not merely a regulatory requirement but a strategic necessity in today's highly competitive and quality-conscious marketplace.
As we've discussed, mock recalls not only help businesses refine their recall procedures but also ensure they can respond swiftly and efficiently in times of crisis. By making mock recalls a routine practice, organizations can instill a culture of preparedness and accountability within their teams, ensuring that everyone understands the critical importance of recall management.
In an era where consumer trust and brand reputation are paramount, businesses that prioritize and invest in mock recalls are better positioned to weather the storms of unexpected product issues. It is a wise investment in both the short and long term, demonstrating a commitment to safety, quality, and transparency.
By integrating mock recalls into their regular operations, businesses are taking a proactive step that can help protect not only their bottom line but also the trust of their valued customers. When the health and safety of your customers and your brand’s reputation are on the line, you can’t take risks.
You need something you can trust and rely upon.
RiskX1 by CMX1 is the solution global brands depend upon. It comes stocked with critical features that allow you to act swiftly, accurately, and efficiently through:
- Automated identification of issues and trends
- Quick identification of impacted parties
- Full cycle event management
- Automated communication and response management
- Real-time event monitoring
- Comprehensive record keeping
Don’t leave your brand vulnerable any longer. Check out this best practice guide: The Definitive Guide to Building a Product Recall Program for more information. Or if you’re ready for a conversation, please reach out.