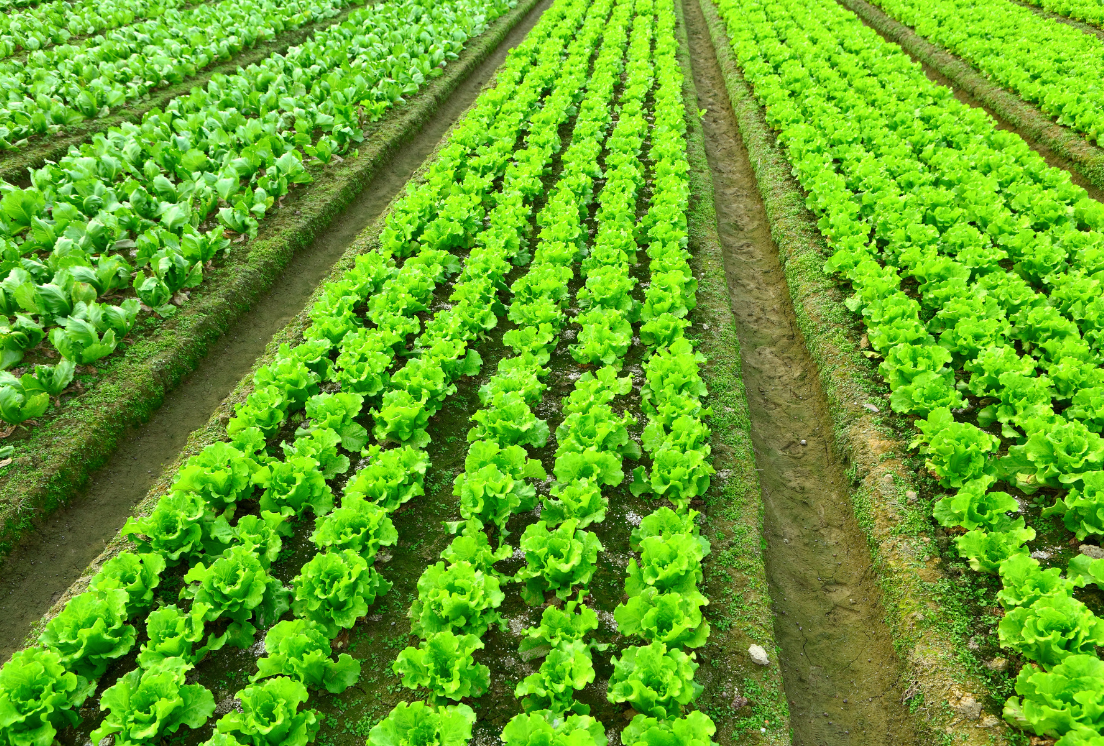
Your food travels a great distance before it lands on your plate, making numerous stops along the way. Here’s how food traceability makes sure it gets there safely.
Consumers account for many factors when deciding which food products they should buy, and they’re becoming increasingly concerned about where their food comes from.
In this article we’ll take a look at the importance of traceability in the supply chain, and how properly functioning food traceability rules can mitigate against outbreaks of food-borne illnesses to ultimately keep consumers safe
What is food traceability?
Food traceability involves tracking the movement of any specific food product throughout the entire supply chain: from growing/production and processing/transformation, right through to distribution, retailing, and consumption.
With so many stops along the way (and so many people involved), there’s ample opportunity for things to go wrong.
Why Food Traceability Matters
Supply chains are getting more and more complex, often involving suppliers and distributors from all over the globe. And with 48 million Americans getting sick each year, it’s no wonder that food traceability has become such a hot topic over the last few years.
A food supply chain comprises all the stages that food goes through, from its start at the grower/creator/supplier right to the end, i.e., the consumer. Starting from the producer (or grower, if it originates from a farm), food is processed or transformed, then transported and distributed to wholesale or retail facilities, and ultimately consumed by your customers.
Considering that food travels on average an estimated 1500 miles to get to the consumer, it’s no wonder that food traceability is a critical consideration for food safety. Plus, recalls and undeclared allergens often get added to the mix, and this further stresses the importance of having impeccable supply chain traceability.
The new era of food safety
Traditionally, pen and paper-based systems were used to track food items as they moved along the supply chain, following the “one-up-one-back” approach. In other words, supply chain visibility extended only to a manufacturer’s direct suppliers (one-back) and the recipients of the food product (one-up).
While this method did provide some information for recordkeeping and traceability, there were some major limitations. Firstly, the recordkeeping systems were mostly paper-based and did not take into consideration the technological advances of the 21st century.
Secondly, every system had its own “language”—in other words, it lacked a universal language to ensure that everyone was on the same page, should any problems occur.
Finally, the limitations of the one-up-one-back approach meant that you were essentially limited to the information of suppliers directly behind you, and receivers directly in front of you. This essentially excluded information on second and third tier vendors, which greatly hinders traceability, especially with product recalls.
With supply chains evolving at an accelerated pace, regulatory approaches had to change.
“We looked at traceability rules all over the world…and they were written very much for the 20th century”. Frank Yiannas, Deputy Commissioner for Food Policy and Response, FDA.
Recognizing the many stages in the supply chain and the need for a universal lexicon, in 2021 the FDA announced the proposed rule for Food Traceability as part of their New Era of Smarter Food Safety Blueprint, and as a response to Section 204 of the FDA Food Safety Modernization Act (FSMA) which deals with food and supply chain traceability.
Instead of the traditional (and very limited) approach, this new rule focuses on key data elements (KDEs) and critical tracking events (CTEs), which will set a foundation for end-to-end food traceability throughout the whole supply chain.
While the FSMA Rule 204 will go into effect in 2023, the FDA is giving companies a period of two years to comply. This means that food businesses have until 2025 to become fully compliant. They should, of course, not wait until then before they start implementing a solution. Once Rule 204 is in full effect, the FDA can require traceability records to be available within 24 hours of a request—by no means an easy task!
Section 204 of the FDA Food Safety Modernization Act—What to Expect
Besides the regulations already in place, under the Food Traceability rule, the FDA will require additional traceability recordkeeping for persons who grow, manufacture, transform, pack, ship, or sell foods on the Food Traceability List (FTL).
The FTL is a list of foods that are considered high risk—foods often associated with either outbreaks or recalls (these include foods like cheese, eggs, fresh melons, freshly cut fruits and vegetables, nut butters, and so forth).
Say for instance you produce jars of peanut butter. Peanuts are not on the FTL, but nut butters are. Therefore, you would be subject to the rule. The same applies for tomato sauce. While tomato sauce is not on the FTL, fresh tomatoes are, and therefore you’d be required to keep records associated with it.
As mentioned, other important components of the Food Traceability List include:
-
Critical Tracking Events (CTEs) - An event in the food supply chain involving the growing, receiving, transforming, creating, or shipping of the food. Any time a food is transformed, or changes hands from one owner to another, it’s considered a CTE.
-
Key Data Elements (KDEs) - Information associated with a CTE for which a record would have to be established and maintained. Examples of KDEs include traceability lot codes, purchase orders, product shipping dates, or product descriptions.
The KDEs required would vary depending on the CTE being performed. Records required at each CTE must contain and link the traceability lot code of the specific food to the relevant KDEs. This code remains the same as the food product moves through the supply chain, unless a transformation of the food occurs.
These requirements only apply to foods that are on the FTL, and includes foods that have listed foods as ingredients. There are some exemptions. If, for instance, your product includes a kill-step, you will need records of the kill-step, but no additional records for steps thereafter.
Clearly recordkeeping is extremely important, and must be maintained in either paper or digital format. No matter how you sort it, you must be able to provide the FDA with an electronic sortable spreadsheet within 24 hours of an outbreak or recall, should they require it—so if you’re currently using paper based records, or a spreadsheet solution, now is a good time to start planning a fully digital approach.
If you have a unique coding system or reference codes, you will need to provide these too, so that the FDA has everything they need to understand your system. This quick turnaround time is a very tall order if your system is still based on pen-and-paper methods, but not so for digital platforms.
Benefits of a food traceability system
As supply chains become more globalized and complex, so too does the risk of food-borne illnesses and recalls. Therefore, the new rule for food traceability is much welcomed in our current times.
Having a standardized system across the industry will have numerous benefits: better recordkeeping, improved communication, rapid identification, and a faster response time in the case of an outbreak or recall, to name a few. It will also reduce the scope of a recall, thereby preventing the recall of products that aren’t necessarily contaminated.
Traceability—The Way Forward for Your Business
Many businesses already have some sort of traceability system in place, but often, the difficulty comes in with sharing the information. This becomes even more difficult when your traceability system relies on paper-based systems.
With the right software, traceability can be as quick as the click of a button. Providing the correct information to the FDA, and providing it quickly, can go a long way in establishing a reputable relationship with the FDA in going forward.
By establishing a good relationship with the FDA, you increase your own business’ credibility and reputation, and if consumers perceive that your business is well-ordered and your food is safe, then it will be easier to gain their trust.
CMX1 + Mojix = a partnership for better food traceability
In 2021, Mojix was selected by the U.S. Food & Drug Administration (FDA) as one of 12 worldwide winners in the FDA’s Low- or No-Cost Tech-enabled Traceability Challenge, which encourages the development of cost-effective traceability solutions for human and animal food operations of all sizes. Mojix is a global leader in item-level intelligence solutions, and recently launched the first open data access, item-level food traceability platform.
CMX1 is the first EQMS solution provider to integrate with this platform.
Mojix’s software as a service-based solution enables tracing of Key Data Elements and Critical Tracking Events along the supply chain. This allows for item-level and lot code traceability when outbreaks of foodborne illness or recalls arise, meeting the proposed rule 204 of FDA’s Food Safety Modernization Act.
Want to know more about the first open-access food traceability platform? Check out the press release.